镗孔加工精度高,内孔车削受孔径长度限刀具选择,需优化加工方案。切削力、刀具设计、夹持方式等影响加工质量。刀具磨损、加工误差、表面质量及测量误差需关注。镗孔加工的精度非常高,精镗孔的尺寸精度可达IT8~IT7,可将孔径控制在0.01MM精度以内。若为精细镗孔,加工的精度可达TT7-IT6,表面质量好。一般的镗孔,表面精糙度Ra值1.6~0.8μm。镗孔是一种高精度的加工工艺,其尺寸精度可达到IT8至IT7,意味着孔径的控制在01毫米以内。若需要更精细的加工,如精细镗孔,其精度可提升至TT7至IT6,同时表面质量也十分出色。一般而言,镗孔的表面粗糙度Ra值介于6至8微米之间。镗加工能够提高孔的同轴度和圆度,使得零部件之间配合更加精确。嘉兴内外圆孔镗加工参考价
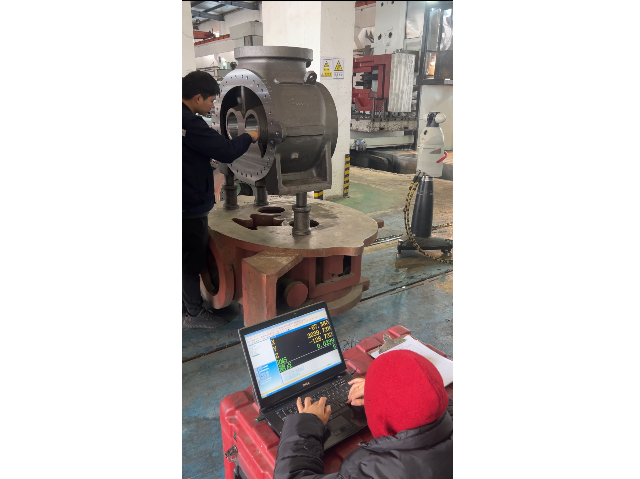
切屑的有效排出:内孔车削加工中,排屑对于加工效果和安全性能的影响也非常重要,特别是在加工深孔和盲孔时尤为如此。较短的螺旋屑是内孔车削较理想的切屑,该类型切屑比较容易被排出,并且在切屑折断时不会对切削刃造成大的压力。加工时切屑过短,断屑作用过于强烈,会消耗更高的机床功率,并且会有加大振动的趋势。而切屑过长会使排屑更困难,离心力将切屑压向孔壁,残留的切屑被挤压到已加工工件表面,就会出现切屑堵塞的风险进而损坏刀具。因此,进行内孔车削时,推荐使用带内冷的刀具。这样,切削液将会有效地把切屑排出孔外。加工通孔时,也可用压缩空气代替切削液,通过主轴吹出切屑。扬州高速钻镗加工行价可调式镗刀能微调切削刃位置,适用于高精度孔的加工。
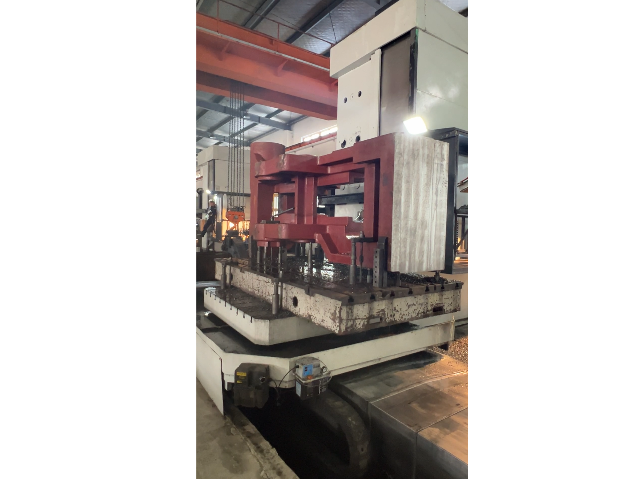
表面质量:镗削已加工表面的鱼鳞状或螺纹状切纹,是比较常见的表面质量现象:主要因刀具的进给和转速不匹配造成:主要因镗削加工的刚性振动及刀具磨损。造成调整失误:镗削加工中由于需要操作人员调整分配层吃刀量,在调整分配进刀余量过程中因操作不当易引发加工尺寸精度偏差。测量误差:镗削加工中、加工后测量过程的量具使用不当、测量方式错误,是镗削加工中常见的质量隐患。1、测量工具失误;2、测量方法不正确。另外,选择合适的刀片槽型和切削参数,也有助于切屑的控制和排出。
在镗孔加工过程中,由于刀具需要连续切削,因此容易出现磨损和破损的情况。这种磨损不仅会降低孔加工的尺寸精度,还会导致表面粗糙度值的增加。同时,如果微调进给单元的标定出现异常,就会引发调整误差,进而影响加工孔径的准确性,甚至可能引发产品质量问题。此外,刀片刃口的磨损变化也是一个需要密切关注的问题。镗刀(镗杆)长径比过大导致加工刚性不足:这需要减少长径比、增加削刚性或调整切削参数。微调进给余量出错:为避免此类问题,应确保每刀进量都经过专人核对并仔细记录。测量方式不正确或校对不仔细:这要求操作人员严格按照标准进行测量,并仔细校对结果。在新材料研发过程中,实验室也常使用小型镗床进行样品测试与验证。
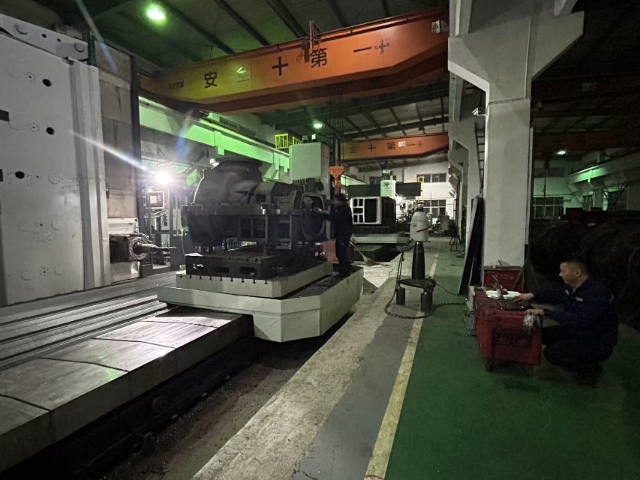
产品特点:1、Y轴双导向系统,该机床立柱设计近似于精密座标镗,Y轴在导轨正面和侧面的复合双导向系统,使主轴箱与导轨7个表面接触,从而可使机床垂切,同时在圆弧插补和轮廓铣削时具有高的精加工精度。2、三轴导轨副采用淬硬磨削矩型导轨,滑动面粘贴美国进口的TurciteB-HP耐磨软带,接触刚性高。3、油气润滑系统可使主轴轴承得到恒定和可靠的润滑,提高轴承的寿命,使主轴精度长期稳定。4、进给单元采用大直径的双螺母滚珠丝杠,在两端施加预紧,可消除热伸长造成的精度损失。在批量生产中,通过优化工艺参数,可以明显提升镗加工效率与质量稳定性。嘉兴内外圆孔镗加工参考价
镗刀具的涂层处理可以降低摩擦系数,提高耐磨性,从而延长使用寿命。嘉兴内外圆孔镗加工参考价
在镗孔加工中,常见的质量问题及其产生原因和解决方案如下:尺寸精度超差:这可能是由于粗镗时余量过大,导致精镗时微调进给余量不准确。为了解决这一问题,需要调整半精镗和精镗的余量,确保镗削状态的稳定。精镗切削深度不够:这通常需要复查对刀情况,并适当调整切削深度。刀刃磨损导致尺寸变化:为确保尺寸精度,应定期更换刀片。镗杆刚性不足产生让刀:此时,应更换刚度更好的杆或适当减少镗削用量。机床主轴径向圆跳动过大:这需要在精镗前确定稳定的跳动差值,并补偿微调量。或者,反馈给设备部门进行调整。嘉兴内外圆孔镗加工参考价
文章来源地址: http://jxjxysb.yybyjgsb.chanpin818.com/jwjjg/jijiagong/deta_27506773.html
免责声明: 本页面所展现的信息及其他相关推荐信息,均来源于其对应的用户,本网对此不承担任何保证责任。如涉及作品内容、 版权和其他问题,请及时与本网联系,我们将核实后进行删除,本网站对此声明具有最终解释权。