机加工工艺探秘:在制造业领域,机加工工艺一直扮演着至关重要的角色。通过了解不同的机加工工艺,我们可以更深入地掌握精密零件制造的奥秘。其中,线切割技术作为一项关键工艺,尤其引人瞩目。它采用黄铜线或钼丝作为电极,通过精确控制切割路径,实现高精度和优良表面光洁度的加工效果。机加工,作为机械加工的精简表述,涵盖了通过机械方式对材料进行精细处理的工艺。其主要在于利用机床对原始材料进行深入、细致的加工。根据不同的加工手法,机加工又可分为手动与数控两大类。刨削用刨刀直线往复运动切削工件,适合加工平面、直槽等简单形状。金华零件机加工原理
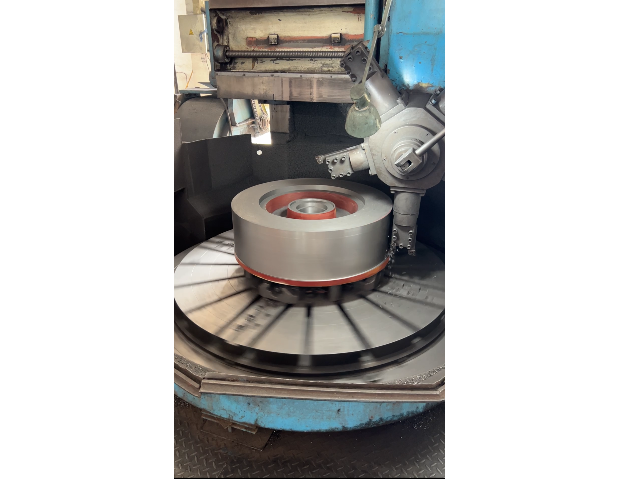
机加工的应用:机加工在现代工业中有着普遍的应用。以下是几个典型的机加工应用领域:1. 汽车制造业:汽车制造过程中需要大量的机加工零件,如发动机缸体、曲轴箱、齿轮等。这些零件需要经过精确的机加工才能达到所需的形状和尺寸精度,从而确保汽车的性能和安全性。2. 航空航天:航空航天领域对零件的精度和质量要求极高。机加工技术在这一领域发挥着关键作用,用于加工飞机和航天器的发动机零件、结构件等。3. 电子设备:电子设备中的许多部件需要通过机加工来制造,如集成电路基板、连接器、散热器等。这些零件的尺寸精度和表面质量对电子设备的性能和可靠性至关重要。4. 医疗器械:医疗器械的制造过程中也需要应用机加工技术。例如,手术器械、牙科工具、人工关节等都需要通过精确的机加工来保证其功能和使用安全。常州不锈钢机加工工艺能解决零件装配间隙问题,通过精确加工保证零件间配合精确。
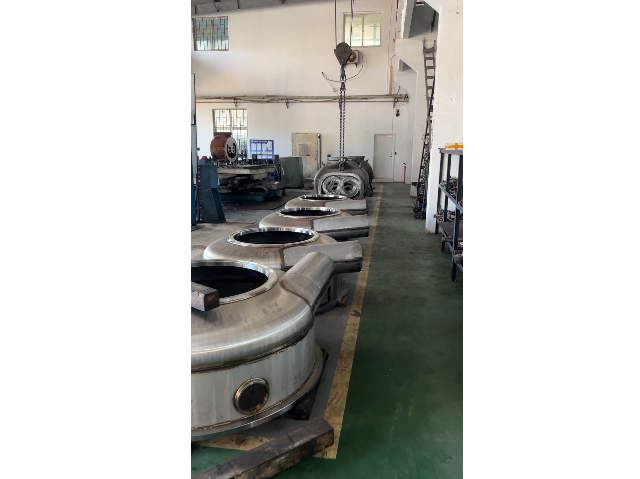
无论是慢走丝还是中丝工艺,都展现了线切割技术在精密零件制造方面的突出能力。1)对于精度要求小于0.05mm的孔,普通铣削无法满足需求,此时需要采用CNC加工技术。若为通孔,则可考虑线切割工艺。2)经过淬火处理的精孔(通孔)需进一步采用线切割进行加工;而盲孔则需在淬火前进行粗加工,淬火后再进行精加工。非精孔在淬火前可按要求完成加工(需留出淬火余量单边0.2mm)。3)宽度小于2mm的槽以及深度较大的3-4mm槽,均需采用线切割进行加工。4)淬火件在粗加工时,应至少保留0.4mm的余量;而对于非淬火件,粗加工的余量可控制在0.2mm。5)镀层的厚度通常介于0.005至0.008mm之间,加工时应参照镀前的尺寸进行。
数控加工(numerical control machining),是指在数控机床上进行零件加工的一种工艺方法,数控机床加工与传统机床加工的工艺规程从总体上说是一致的,但也发生了明显的变化。用数字信息控制零件和刀具位移的机械加工方法。它是解决零件品种多变、批量小、形状复杂、精度高等问题和实现高效化和自动化加工的有效途径。数控加工是指,由控制系统发出指令使刀具作符合要求的各种运动,以数字和字母形式表示工件的形状和尺寸等技术要求和加工工艺要求进行的加工。它泛指在数控机床上进行零件加工的工艺过程。能解决零件表面粗糙度问题,经抛光等处理让表面光滑美观且耐用。
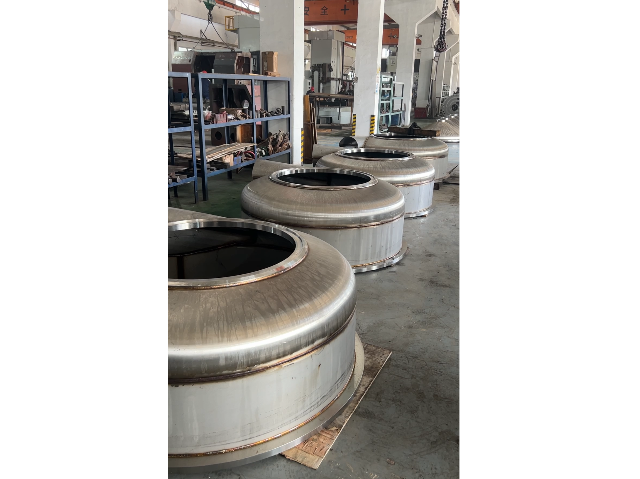
常见的机械加工设备与工具:1 车床与铣床,车床和铣床是机械加工中较常见的设备。车床主要用于车削操作,通过旋转工件并使用固定的切削工具去除材料,适用于制造圆柱形零件。铣床则使用旋转切削工具来去除材料,能够加工平面和复杂形状。数控机加工(CNC)技术的应用,使得这些设备能够实现高精度和高效率的加工操作。CNC车床和铣床通过预先编程的指令控制切削工具的运动,确保加工过程中每一步都精确无误。2 钻床与磨床,钻床和磨床也是机械加工中不可或缺的设备。钻床使用旋转钻头在工件上创建圆孔,通常作为其他加工工序的准备步骤。磨床则使用磨轮去除材料,主要用于提高工件表面的光洁度和精度。磨削过程能够去除极小量的材料,适用于需要高精度和高表面质量的零件加工。能解决复杂零件加工难题,如航空发动机叶片,实现高精度成型。杭州弯折件机加工供应
超声波加工可加工硬脆材料,利用超声波振动辅助切削。金华零件机加工原理
数控机床是一种用计算机来控制的机床,用来控制机床的计算机,不管是专门使用计算机、还是通用计算机都统称为数控系统。机械加工过程中常见的挑战:机械加工过程中可能遇到各种挑战,包括:材料选择:不同材料的加工特性不同,选择合适的材料对于确保加工质量至关重要。工具磨损:切削工具在使用过程中会逐渐磨损,影响加工精度和效率。定期更换和维护工具是必要的。热处理:加工过程中产生的热量可能导致工件变形和尺寸变化,需要采取适当的冷却措施。公差控制:确保加工零件的尺寸和形状在允许的公差范围内,是机械加工中的重要任务。金华零件机加工原理
文章来源地址: http://jxjxysb.yybyjgsb.chanpin818.com/jwjjg/jijiagong/deta_27677303.html
免责声明: 本页面所展现的信息及其他相关推荐信息,均来源于其对应的用户,本网对此不承担任何保证责任。如涉及作品内容、 版权和其他问题,请及时与本网联系,我们将核实后进行删除,本网站对此声明具有最终解释权。