旋转清洗球的技术发展,深刻反映了工业清洁领域从人力密集型向智能化、自动化转型的趋势。从初的手动操作到如今的全自动智能控制,每一次技术迭代都为行业带来质的飞跃。早期的手动旋转清洗球,主要依赖人工操作。操作人员需将清洗球安装在设备内,通过外接高压水管注入清洁液,再手动调节阀门控制水流压力和方向。这种方式虽能实现基础清洁功能,但存在效率低、清洁效果不稳定的问题。清洗过程中,难以保证覆盖设备的每个角落,且人力操作强度大,耗时耗力,适用于小型设备或清洁要求不高的场景。随着工业需求升级,半自动旋转清洗球应运而生。这类清洗球通过增加简单的机械驱动装置,如齿轮、轴承,利用水流冲击力带动球体旋转,实现360度动态清洁。相比手动清洗球,其清洁效率提升,能有效减少清洁盲区。同时,半自动清洗球可与管道系统集成,通过阀门控制清洗液的通断和压力调节,部分环节实现自动化,降低了人工干预频率,在食品饮料、制药等行业的中型设备清洁中得到广泛应用。进入智能化时代,全自动旋转清洗球成为行业主流。它集成传感器、微处理器和自动化控制系统,具备智能监测与自适应调节功能。内置的压力、流量传感器实时反馈清洁数据。 旋转清洗球的防水性能好,可在潮湿环境中长期稳定运行。插销旋转清洗球ISO标准
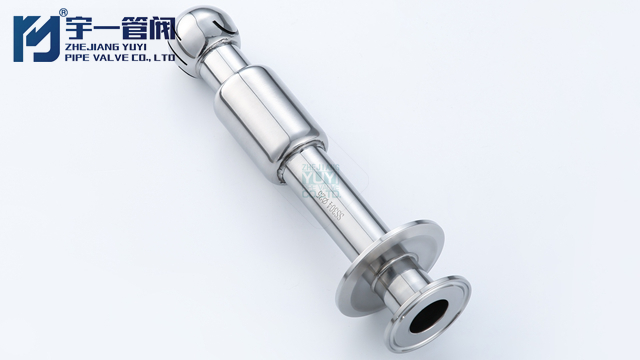
在工业清洁场景中,旋转清洗球运行时产生的噪音不仅干扰工作环境,还可能影响设备寿命与清洁效果。通过创新的噪音控制技术与科学的静音设计,可降低其运行噪音,实现清洁作业的高效与安静。旋转清洗球的噪音主要源于机械部件摩擦、流体冲击和振动。针对这些噪音源,静音设计从结构优化与材料选择两方面着手。在机械结构上,采用高精度加工工艺制造驱动轴、轴承等部件,确保配合间隙极小,减少摩擦产生的噪音。例如,将轴承精度提升至P5级,可使旋转摩擦噪音降低20%以上;同时,优化球体内部流道设计,采用流线型导流槽和光滑内壁,减少清洁液流动时的湍流与涡流,降低流体冲击噪音。材料应用也是噪音控制的关键。在旋转部件接触位置,使用高分子复合材料代替金属部件,这类材料具有自润滑性和减震特性,能有效吸收振动能量。如在轴承座与球体连接处嵌入橡胶减震垫,可阻隔振动传递,降低结构噪音。此外,部分清洗球外壳采用双层复合结构,内层为度金属保证机械性能,外层包裹隔音材料,形成隔音屏障,进一步削弱噪音传播。智能控制技术为噪音控制提供了新途径。通过安装振动传感器与噪音监测模块,实时采集清洗球运行数据,当检测到异常振动或噪音时。 插销旋转清洗球ISO标准旋转清洗球的水流射程远,可覆盖大型储罐内部各个部位。
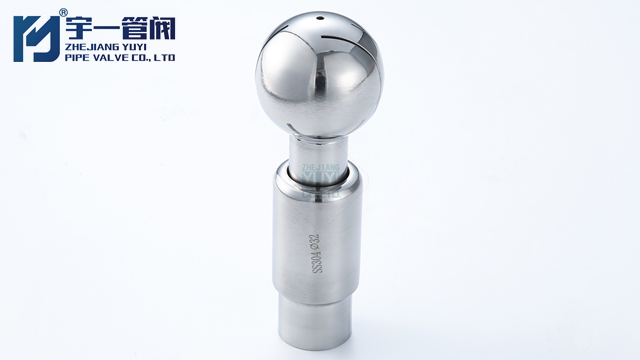
化工生产中,设备长期接触强酸、强碱、有机溶剂等腐蚀性介质,普通清洁工具难以胜任设备清洁工作,极易因腐蚀失效。耐腐蚀旋转清洗球凭借的抗腐蚀性能和高效清洁能力,成为化工设备清洁的。在材质选择上,耐腐蚀旋转清洗球采用特殊材料配方。阀体多选用316L不锈钢、双相不锈钢或钛合金,这些材料不仅具备度和良好的机械性能,更能有效抵御氯离子、硫酸根离子等腐蚀性介质的侵蚀。以316L不锈钢为例,其钼元素含量的提升使其耐点蚀和缝隙腐蚀能力增强,适用于常见的酸碱环境;钛合金则凭借表面形成的致密氧化膜,在强氧化性酸、海水等极端介质中表现优异。隔膜和密封件采用聚四氟乙烯(PTFE)、全氟橡胶(FFKM)等高分子材料,这些材料具有极强的化学惰性,对几乎所有化学品都呈现出优异的耐受性,从根本上避免了清洁过程中因材质腐蚀导致的设备污染和清洗球损坏。结构设计上,耐腐蚀旋转清洗球优化流体通道,减少介质残留与腐蚀风险。其内壁采用镜面抛光工艺,粗糙度极低,避免污垢附着和腐蚀介质滞留;流道采用流线型设计,降低流体阻力,减少清洁液残留,防止局部腐蚀。此外,部分产品还配备可拆卸式结构,便于定期检查和更换易损部件,进一步延长使用寿命。在实际应用中。
乳制品行业对设备清洁的卫生标准近乎苛刻,任何微生物残留或杂质污染都可能导致产品变质。旋转清洗球凭借高效清洁与安全可靠的特性,成为乳制品生产设备清洁的主力军,以下通过实际案例解析其应用成效。在某大型乳制品企业的鲜奶发酵罐清洁中,传统人工清洗需耗费6名工人近3小时,且难以彻底罐壁残留的乳垢与生物膜,导致菌落总数超标风险增加。引入食品级316L不锈钢材质的旋转清洗球后,清洁流程实现自动化升级。该清洗球配备多角度扇形喷嘴,在高压水流驱动下高速旋转,15分钟内即可完成360度无死角冲刷。清洗后检测显示,发酵罐内壁菌落总数从原来的每平方厘米1000CFU降至5CFU以下,完全符合乳制品生产卫生标准。同时,清洁效率提升66%,每年节省人工成本超50万元。在酸奶生产线的管道清洁环节,由于酸奶黏性大,管道内壁易残留蛋白质和糖分,滋生嗜冷菌,影响产品保质期。企业采用内置智能传感器的旋转清洗球,该清洗球可根据管道内污垢浓度自动调节喷射压力与旋转速度。当检测到顽固污垢时,清洗球启动强力冲刷模式,以20bar的高压和400转/分钟的转速,配合碱性清洁剂,快速剥离管道内壁的黏性残留。清洁过程中,系统实时记录压力、温度、时间等参数。 不锈钢材质的旋转清洗球,具有良好的耐腐蚀性,适用于食品、化工等多种行业。
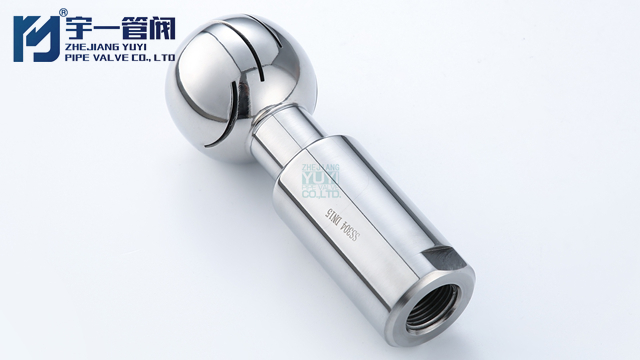
在工业清洁领域,旋转清洗球的3D喷淋技术凭借出色的清洁能力备受青睐。这项技术通过创新的结构设计、精妙的流体力学原理与高效运动模式,实现清洁无死角,成为保障设备洁净的技术。3D喷淋技术的在于多维度的喷射结构设计。旋转清洗球表面分布着多个不同角度、不同类型的喷嘴,包括直射型、扇形和锥形喷嘴等。这些喷嘴并非均匀分布,而是依据设备形状和常见污垢附着位置,进行科学布局。例如,在清洗罐体时,顶部喷嘴采用大角度扇形喷射,覆盖罐顶与侧壁;底部喷嘴则以直射方式,集中冲刷顽固污垢;侧壁喷嘴呈螺旋排保罐体全周向清洁。通过多角度、多类型喷嘴的组合,清洗球在旋转过程中,使清洁液从不同方向喷射而出,构建起立体的清洁网络。流体力学原理的应用是实现3D喷淋效果的关键。当高压清洁液进入清洗球后,内部导流槽根据不同喷嘴需求,精细分配流量与压力。高速旋转产生的离心力,进一步增强清洁液的喷射动能,使其以强劲的冲击力覆盖设备表面。同时,流体在喷射过程中,利用空气动力学原理,形成涡流与湍流效应,增强对死角、缝隙的清洁能力。在管道清洁中,这种湍流效应能深入弯道与接口处,常规喷淋难以触及的污垢。此外。 旋转清洗球的球体表面光滑,不易残留污垢,便于自身清洁维护。插销旋转清洗球ISO标准
旋转清洗球的表面经过特殊处理,不易粘附污垢,清洁更轻松。插销旋转清洗球ISO标准
在实际应用中,旋转清洗球的安装常面临空间狭窄、接口尺寸不匹配等问题,限制其清洁效能的发挥。通过优化设计与灵活方案,可有效应对这些安装空间限制。小型密闭设备是常见的空间受限场景。如实验室反应釜、小型储液罐等,内部空间狭小,传统清洗球难以适配。对此,可采用微型化设计的清洗球,其直径通常在20-50mm之间,通过精巧的结构布局,在有限空间内实现360度旋转喷射。同时,开发折叠式喷嘴,未工作时喷嘴收缩,便于安装;启动后自动展开,扩大清洁覆盖范围。此外,采用柔性管路连接清洗球与外部控制系统,减少刚性连接占用的空间。管道系统安装时,常因管径过小或弯角过多导致清洗球难以布置。针对此类问题,研发出分体式清洗球,其由可拆卸的球体与驱动组件组成,先将球体放入管道,再通过接口连接驱动部分,降低安装难度。对于复杂管路,使用可弯曲的蛇形清洗球,该球体通过柔性关节实现多角度转向,能顺利通过S型、U型弯管,确保管道内部清洁无死角。大型设备虽空间宽敞,但存在安装高度受限、检修口尺寸不足的问题。例如,巨型储罐的检修口直径有限,难以容纳大尺寸清洗球。可设计伸缩式安装支架,将清洗球折叠后通过检修口送入罐内,再自动展开至工作状态。 插销旋转清洗球ISO标准
文章来源地址: http://jxjxysb.yybyjgsb.chanpin818.com/qxqlsbml/qtqxqlsbpy/deta_27731810.html
免责声明: 本页面所展现的信息及其他相关推荐信息,均来源于其对应的用户,本网对此不承担任何保证责任。如涉及作品内容、 版权和其他问题,请及时与本网联系,我们将核实后进行删除,本网站对此声明具有最终解释权。